Case study: Proactive Cooling
Traditional cooling systems operate in a straightforward manner: a chiller cools glycol to a few degrees below the lowest required setpoint, and tanks in the loop request cooling as needed. However, this approach is often inefficient, as only a few tanks may need cooling at any given time, and the chiller constantly runs to maintain a low temperature, even when it’s not required.
Frigid.Cloud’s advanced temperature data monitoring helps optimize cooling by understanding each tank’s needs at different stages of fermentation. This allows for proactive cooling, where the chiller adjusts its setpoint based on the required load, ensuring each tank receives the necessary cooling without wasting energy.
The Proactive Cooling algorithm can be programmed to avoid peak electricity pricing periods, take advantage of excess renewable energy, or reduce overall energy consumption by balancing the cooling needs of all tanks.
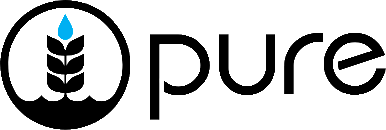
Peak Avoidance Logic at Pure Project in Vista, CA.
With a strong commitment to sustainability and carbon neutrality, Pure Project Brewery has 11 fermenters, 3 Brites, and a cold liquor tank.
Winslow and the team identified a peak electricity period from 4pm to 9pm, which made up 25% of daily chiller consumption, with tariffs 300% higher during this time.
By implementing Frigid.Cloud’s Proactive Cooling algorithm to schedule cooling around peak periods, the brewery reduced its peak electricity usage from 88kWh per day to 30kWh. Overall, daily consumption dropped by 68kWh, cutting their chiller energy costs by 35%.
%
Peak period kWh reduction
%
Daily kWh reduction
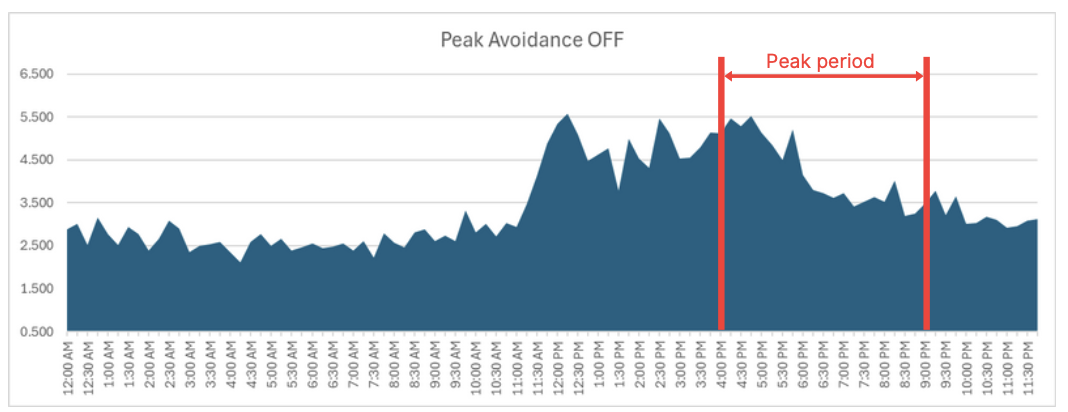
This graph shows the energy profile of the chiller before the proactive logic was applied.
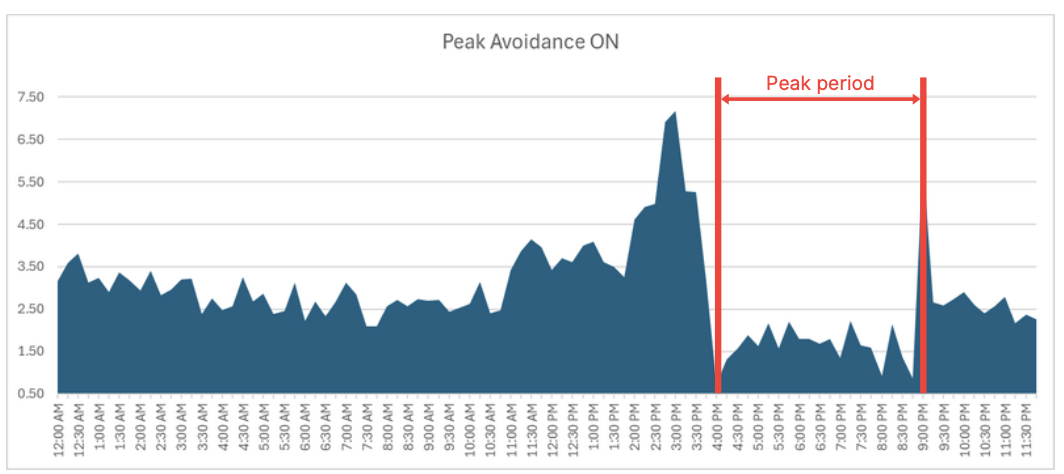
This graph shows the energy profile of the chiller after the proactive cooling was applied. There is a spike of energy use prior to the peak period and followed by a heavily reduced load during the peak period.